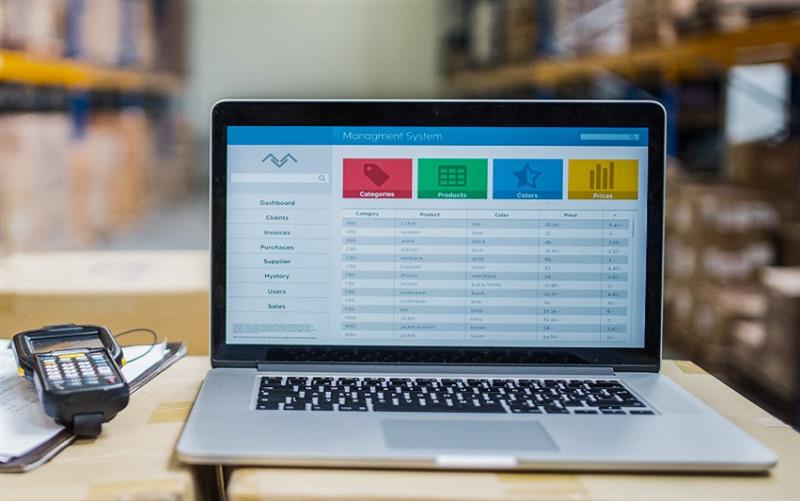
For hospitals, clinics, pharmacies, and other healthcare facilities, efficient management of medical supplies is essential. In the absence of a well-organized system, patient safety hazards, financial losses, and treatment delays may result from stock shortages, theft, misplacements, and compliance breaches.
Through process automation, improved accuracy, and real-time supply control, medical inventory software removes these difficulties. Let's examine in more detail how inventory software guarantees a seamless, effective workflow and revolutionizes medical supply management.
By adopting medical inventory management software, healthcare providers can move from chaos to control, ensuring:
Accurate real-time stock tracking
Automated ordering and restocking
Expiration date monitoring & compliance
Data-driven decision-making
Multi-location inventory control
1. Real-Time Inventory Tracking
Not knowing exactly what is in stock is one of the main issues with medical supply management. Spreadsheets and paper logs are examples of manual tracking techniques that are frequently out-of-date and prone to human error.
This is resolved by inventory software:
Real-time stock updates: All supply movements, including ordering, receiving, using, and disposing of, are tracked in real time.
Barcode and RFID scanning: Barcodes and RFID tags make it simple to trace supplies, which lowers theft and misplacement.
Cloud-based monitoring: Employees may use any device to view inventory levels, facilitating prompt decision-making.
For instance, when new drugs are delivered or dispensed, a hospital pharmacy can use barcode scanning to rapidly update its stock levels, avoiding inconsistencies and overstocking.
2. Automated Reordering & Stock Level Optimization
While some healthcare institutions lose money overstocking commodities that expire before usage, many suffer from stock shortages as a result of neglected or delayed orders.
How Inventory Software Addresses This:
Auto-reorder thresholds: When supply levels fall below a certain threshold, the system automatically initiates restock orders.
Demand forecasting: Order quantities are optimized and future demand is predicted based on historical usage data.
Supplier integration: Pre-approved vendors can receive orders directly, guaranteeing prompt and effective refilling.
As an illustration, a busy surgical institution establishes a minimal standard for disposable gloves. The system automatically initiates an order with the preferred provider when stock drops below this threshold, guaranteeing ongoing availability without the need for human involvement.
3. Expiration Date & Compliance Management
Both patient safety and regulatory compliance are seriously jeopardized by expired medical products. Many facilities have trouble manually keeping track of expiration dates, which can result in waste or, worse, inadvertent use of products that have expired.
This is resolved by inventory software:
Expiration date tracking: Employees are alerted when products are about to expire, and supplies are recorded with expiration dates.
By ensuring that older goods is used first, the First-In, First-Out (FIFO) method helps to reduce waste.
Documentation ready for compliance: For audits, the system keeps an electronic record of product consumption, storage conditions, and regulatory compliance.
For instance, a pharmacy can save waste and ensure compliance by using or returning pharmaceuticals before they become unusable by using automated alerts when they are about to expire.
4. Enhanced Data Analytics & Reporting
Medical supply decisions are frequently made on the basis of conjecture in the absence of precise facts, which can result in overpaying, ineffective ordering, and supply mismatches.
How Inventory Software Addresses This:
Cost analysis & Usage Trends: Determines which supplies are most frequently utilized and where expenses might be cut.
Inventory waste tracking: This aids in identifying needless losses and improves purchasing choices.
Regulatory reporting: Produces reports required for internal reviews, insurance claims, and compliance audits.
As an illustration, a hospital examines its inventory statistics and finds that a certain brand of syringes is frequently wasted because of flaws in the packaging. Every year, they save thousands of dollars by switching suppliers.
5. Multi-Location & Remote Inventory Management
Tracking supplies across numerous locations is a challenge for healthcare providers with multiple locations, such as clinics, hospitals, or mobile health units.
How Inventory Software Addresses This:
Centralized inventory control: Real-time stock updates are available across numerous locations via a single dashboard.
Inter-facility transfers: Extra supplies at one place can be effectively moved to another that needs them.
Remote access: Employees may make orders and check stock levels from any device, facilitating quick decision-making.
As an illustration, a healthcare system comprising several hospitals transfers extra personal protective equipment (PPE) from one facility to another using a common inventory platform, thereby cutting expenses and waste.
6. Theft & Loss Prevention
Medical supplies are susceptible to theft, loss, or illegal use, particularly expensive products like painkillers, specialty medications, and surgical instruments.
How Inventory Software Addresses This:
User tracking & Access Control: Only authorized personnel are able to request or access high-risk products.
Audit logs and tracking: Complete accountability is established by recording every item's movement.
Unusual activity alerts: To stop theft and misuse, the system recognizes and flags abrupt changes in inventory.
For instance, a hospital pharmacy observes unforeseen variations in the quantity of opioids in stock. They can detect unwanted access, take remedial action, and stop additional losses via digital tracking.
7. Supplier & Vendor Management
For medical supplies, healthcare providers depend on a number of vendors; yet, major interruptions may result from price volatility, variable quality, and delayed deliveries.
How Inventory Software Helps:
Vendor performance tracking: The system keeps tabs on product quality, delivery time, and supplier dependability.
Automated purchase orders reduce delays by placing orders efficiently.
Optimizing costs can be achieved by comparing vendor prices and historical order data.
For instance, a clinic that reviews vendor performance reports discovers that a particular supplier regularly causes delivery delays. By moving to a more dependable supplier, they increase productivity and decrease downtime.
8. Mobile & Cloud-Based Accessibility
Particularly in emergency situations, healthcare personnel frequently want immediate access to inventory data.
How Inventory Software Addresses This:
Mobile compatibility — Employees may use mobile phones to place orders, scan barcodes, and check stock levels.
Cloud-based access: Allows for remote inventory management, guaranteeing current stock tracking even from off-site locations.
Instant synchronization: Changes performed at one site instantly affect all other locations.
For instance, a cloud-based inventory system allows a mobile health unit responding to a disaster to instantaneously request emergency medical supplies, guaranteeing quicker reaction times.